Best Practices for Coin Cell Assembly#
A key challenges faced by researchers and manufacturers alike is the variability in coin cell assembly procedures, which can significantly affect the cell’s performance and lifespan. To address this issue, there is a growing consensus on the need to standardize the assembly process, with particular emphasis on the timing and amount of electrolyte injection.
The assembly procedure for coin cells involves several critical steps, each of which can influence the final performance of the cell. Among these steps, the timing of electrolyte injection and the precise amount of electrolyte used are crucial. The electrolyte serves as the medium for ionic transport between the anode and cathode, and any inconsistencies in its application can lead to significant performance variations.
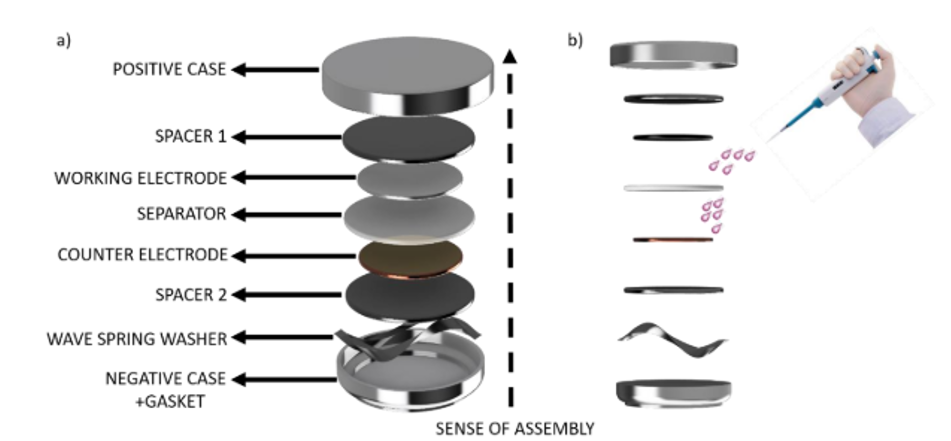
Coin Cell Assembly Diagram#
Timing of Electrolyte Injection#
The timing of electrolyte injection is vital because it affects the wetting of the electrodes and the formation of the solid electrolyte interface (SEI). If the electrolyte is injected too early or too late, it can result in incomplete wetting, leading to poor ionic conductivity and increased internal resistance. Standardizing the timing ensures that each cell receives the electrolyte at the optimal moment, promoting uniform SEI formation and consistent cell performance.
Amount of Electrolyte Injection#
The amount of electrolyte injected into the cell is equally important. Insufficient electrolyte can lead to poor ionic contact and reduced cell capacity, while excess electrolyte can cause issues such as leakage and parasitic reactions. A standardized amount ensures that each cell has the right balance, optimizing performance and longevity.
Key Points:#
Impact of Assembly Procedure: The assembly process significantly affects cell performance, leading to variations in reproducibility.
Electrolyte Volume and Stack Height: Among top-performing cells, there was no clear relationship between electrolyte volume, stack height, and performance.
Influence of Other Factors: Other factors, such as the type of crimping machine used, may also impact capacity and retention.
LRCS Model: The LRCS (CNRS) assembly method used less electrolyte volume and a lower stack height compared to other methods.
Procedure: Follow the model shown in Figure 2, placing one stainless steel spacer between each electrode and the closest case.